Bio-Packaging Details
Manufacturing Facilities
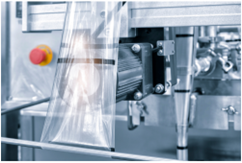
- Blown Film Extruder
A blown film extruder produces thin plastic films by melting and extruding polymer materials through a circular die, then inflation into a tubular film using air. For bio-packaging, it is utilized to create films from biodegradable polymers (like PLA or PHA) due to its ability to produce uniform, flexible, and eco-friendly packaging materials that reduce plastic waste and environmental impact.
- Continuous Film Casting
Continuous film casting is a process in which a molten polymer or polymer solution is spread onto a moving substrate, cooled, or dried to form a uniform thin film. It is used in packaging to produce smooth, biodegradable films from materials like starch, chitosan, or PLA. These films offer excellent barrier properties and sustainability for food packaging and other eco-friendly applications.
- Film Rolling
Film rolling is a process that involves flattening and thinning a polymer film using rollers to achieve a uniform thickness. For bio-packaging, it is used to process biodegradable materials like PLA, PHA, or starch-based polymers into consistent films, ensuring durability and flexibility for eco-friendly applications like food wraps and packaging.
- Paper Plates and Cups Making
Paper-based products are formed using dies and heat. It is used for bio-packaging to produce eco-friendly, biodegradable, and compostable alternatives to plastic tableware, reducing environmental pollution while meeting food-grade packaging needs.
- Film Casting
Film casting is a process where a polymer solution or melt is spread onto a flat surface or moving substrate and then cooled or dried to form a thin, uniform film. It is widely used in bio-packaging to produce biodegradable films from materials like starch, cellulose, or PLA, offering excellent transparency, flexibility, and barrier properties for sustainable food packaging and other eco-friendly applications.
Testing Facilities
- Mechanical Properties
A tensile testing machine directly measures the ultimate tensile strength, breaking strength, maximum elongation, and area reduction of the prepared packaging materials.
- Barrier Properties
Barrier properties refer to the packaging's ability to resist light, moisture, and oxygen absorption. Barrier properties are essential for maintaining food quality and safety. Packaging systems with optimal barrier properties protect their contents against water vapor, gases, light, and aroma compounds, therefore ultimately against deterioration.
- Thermal Properties
Thermogravimetric analysis was done to measure the composition, purity, decomposition reactions, decomposition temperature, and absorbed moisture content of the packaging material. TGA provides quantitative measurement of mass change in materials associated with transition and thermal degradation.
- Biodegradability and Toxicity Assessment
This testing of packing material was performed to find whether the developed material was compostable or biodegradable, ensuring it will not lead to any detrimental effects on the ecosystem or natural habitats.
- Surface Properties
A contact angle goniometer measures the angle formed between a liquid droplet and a solid surface, providing insights into surface wettability and hydrophobicity/hydrophilicity. It is crucial for assessing the surface properties of bio-packaging materials, such as adhesion, and coating quality ensuring optimal functionality and compatibility.